Concrete is used in various areas around our homes. It is a durable material, but it is not indestructible. It is important to fix damaged concrete before it causes structural problems.
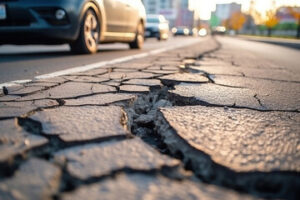
The best way to Concrete Repair Morgantown WV is by using the right concrete repair materials. These materials must have the right ingredients, texture and cost.
Concrete repair jobs involve a variety of surface preparation techniques depending on the geometry and structural requirements. For example, some cracks are dormant and not structural but they need to be routed and sealed so that water doesn’t infiltrate.
In this situation, contractors can use a commercial-grade concrete sealant with a wide range of hardness and flexibility properties to meet the needs of the project. The key to a successful crack sealant is proper preparation, such as high pressure air blasting the crack to remove dirt, dust, loose debris and any contaminants like paint or oil that may break the bond between the repair material and the concrete.
Contractors can choose from a number of repair materials that include epoxies, silicones and polyurethanes. Each material has its own characteristics, such as tensile strength, moisture tolerance and crack movement tolerance. For instance, a low-modulus epoxy’s ability to expand and contract with the movement of concrete cracks will help maintain a stable repair while a high-modulus urethane can handle significantly more movement.
Epoxy injection binds or welds cracks with widths as narrow as 0.002 in together, restoring the concrete’s integrity including its stiffness and strength. It is most effective for repairing wet and leaking cracks with a ductility that can accommodate future movements of the concrete structure.
This repair option requires a high degree of technical skill and equipment to be performed correctly. It is also more expensive than other repairs, but it’s an excellent choice for addressing the root cause of a concrete problem.
Epoxy injection requires drilling holes at close intervals along horizontal, vertical or overhead cracks. A non-sag epoxy is then injected through the ports and into the crack to fill and seal it. Moisture tolerant epoxies are available, but they will not restore as-design strengths and can’t resolve cracks caused by corrosion or design errors.
Stitching
Stitching concrete repair jobs involves the use of carbon fiber grid stitching embedded into a structural epoxy adhesive. It is considered a true structural concrete crack repair technique that actually helps slow down or stop concrete from continuing to crack, and has proven to be very effective in both commercial and residential applications. The system is also very cost-effective compared to other concrete repair methods and offers a full warranty against future cracking.
As a concrete repair technician, you’ll be working on your own for most of the workday, so it’s important to have an independent mindset and take responsibility for the projects that are assigned to you. Showing that you can manage these repairs without the help of a supervisor will allow you to advance in your career, and may even open up new pathways into management or franchise ownership.
Depending on the type of concrete surface that needs to be repaired, different repair techniques will be required. Common small concrete repair tasks include spalling repair, joint repair and slab jacking, levelling and decorative repair. Spalling is the process of deterioration of concrete, which leads to a rough or pitted surface and requires filling and patching to repair it. Joint repair can be done by re-colking or re-grouting, and is usually done to improve the appearance of the concrete structure. Levelling involves injecting a grout mixture under the concrete to raise it back to its original level, and decorative repair can be done by applying a coat of sealant to enhance the look of the concrete.
A successful concrete repair job requires proper preparation of the area to be repaired. This includes cleaning the existing surface, if necessary, and making sure that all factors that contribute to cracking are addressed in the repair design. It’s a good idea to walk-through the repair area with your repair contractor to discuss these issues and determine how they will be addressed in the actual repair job.
Having the right tools and equipment for a repair job will also be crucial to its success. For example, a concrete repair contractor should have a variety of tools, such as a caulk gun, paddle mixer, a wire brush and a number of hand trowels (including a finishing trowel, margin trowel and pointed trowel). A good concrete repair mix manufacturer will provide contractors with a product that is designed specifically for the job in question. Using the correct product for each repair job will prevent the concrete from being damaged or failing prematurely.
Prestressing
Whether it’s a concrete slab forming a sidewalk or an old parking garage column, the same basic principles apply to any concrete repair job. The first step is determining the cause of the problem, which could include destructive testing to reach reinforcement and find any indication of corrosion. Then, the contractor can address the issue.
Often, structural concrete is designed to be reinforced with steel bars or rods to support heavy loads and reduce deflection. However, a more innovative approach to this construction material is the introduction of internal stresses into the concrete to better resist the tensile forces that can result from loading. This is known as prestressed concrete, which has its origin in bridge building and has become more common in structures such as commercial buildings and parking garages.
The concept of this method is similar to stacking books together, then pressing tightly on both ends. The end result is a much stronger unit that can support great weight from both sides without falling apart. This is the idea behind prestressed concrete products, which can also span great distances and use less concrete than traditional reinforced concrete beams.
Concrete can be prestressed during its production through a process called pre-tensioning or post-tensioning. In this form of the construction material, curved ducts are formed into the concrete and steel tendons, usually high-strength wires or alloys, are then pulled tight and anchored externally to achieve a prestressed state before the concrete is poured and cured. This internal stress balancing of strengths is beneficial to the overall strength of the structure, allowing it to better resist lateral and torsional stresses.
Dry Packing
A dry pack concrete repair job involves filling the gap with mortar that has been pre-blended and is ready to use. The mix contains masonry sand, Portland cement and water. It differs from normal concrete in that it does not contain aggregate like pebbles, which makes it more dense and able to withstand pressure from water better. Dry-pack mortar is often used in repairing basement walls and has many other uses around the home.
The mortar is placed in layers and compacted with a hardwood stick. A groove is put on the surface of each layer to help with bonding with the surrounding concrete. A minimum of 14 days must be allowed for the repair to cure.
For a small project, dry pack can be mixed in a wheelbarrow with a shovel. However, large projects may require a portable mixer that will save time and effort. A concrete mixer with a drum attachment can be used to create a consistent mix, and it is possible to add in some water as needed. When mixing, safety precautions should be followed to avoid breathing in dust and dirt particles. A pair of gloves, safety goggles and a face mask are all recommended.
If a machine is being used to apply the mortar, the operator should make sure it is a good quality, with a good motor. The machine must also be kept clean and free of oil and other contaminants that could contaminate the mix. A high-quality machine will have a low noise level and produce very little air pollution.
During the drying process, moisture-sensitive plastic surface-mount devices should be kept in moisture barrier bags to prevent popcorn cracking. This occurs when the internal moisture of the plastic package vaporizes rapidly during board mounting and causes the device to crack. Moisture ingress into the plastic is also a major cause of corrosion in industrial machinery and equipment. This is another important reason why a professional should always inspect equipment and repair any damaged components.